IndustraCare's Workplace Considerations series shines a light on different aspects of day-to-day health and safety management, with tips and techniques for development.
Everyone's heard of risk assessments, these massively time consuming, horrendously inconvenient pieces of red tape which create endless headaches, stress and misery.
At least this is what I built it up to be in my head. The first risk assessment I had to carry out was for an independent restaurant where I was a waiter. I was working front of house one particular day (which was a rare occasion), when I answered the phone it was a school wanting to book a school trip, and after going through all the details asked if they could have a copy of our risk assessment. I was stumped, as no one had ever mentioned a risk assessment to me in the restaurant. I told the customer I'd get the information and call her back.
I gave my manager a shout and asked him about the risk assessment, thinking it'd just be a matter of sending a quick email. He left, returning about five minutes later with a big ring binder and dropped it on the counter in front of me. Inside the folder were pages upon pages of legal jargon. 'You have thirty minutes' he said while walking away.
He expected me to carry out a full risk assessment with no previous experience of either health and safety or working in a restaurant, within 30 minutes nonetheless.
So what's the risk assessment all about?
Well, first of all it isn't about creating a massive ring binder full of paperwork that everyone dreads looking at. Instead we're interested in creating sensible approaches to risk management, keeping everyone that could be affected by the actions of your organisation safe. This includes your staff, customers, contractors or the general public for example.
In its most basic form, a risk assessment means thinking about what could cause harm and ways you can control these potential harms. Remember, if you have fewer than five employees you don't need to record your risk assessment. However we would recommend you do so anyway, to refer back to in the future to see if your controls are working.
We need to be looking a the real risks and those which are most likely to cause harm.
So we're now going to look at the five steps to carrying out your own risk assessment, but before we do its worthwhile to remember:
- a hazard is anything that may cause harm, such as chemicals, electricity, working from ladders, an open drawer etc.
- the risk is the chance, high or low, that somebody could be harmed by these and other hazards, together with an indication of how serious the harm could be.
Step 1: Hazard Identification
Take a walk around your workplace, (we'd recommend taking a clipboard to make writing easier) and specifically look for hazards. Think about the activities, people, processes and equipment in your workplace that could cause harm.
Another way of identifying the potential hazards is to read up on manufacturer's instructions or data sheets which have been provided, as they will usually explicitly tell you the hazards created. This is particularly useful when it comes to machinery or chemicals for example. Note that not all hazards are always stated.
Now we've got a basic idea of the hazards we're going to have to control, it's now worth looking back at past records which will show patterns, as well as pointing out less obvious hazards.
You must also take account of activities which may not be considered a day-to-day activity or are considered non-routine. These can include, for example, cleaning, maintenance or changes in production factories, for example a meat factory which produces both beef and lamb, the production line must be cleaned down in between cycles.
Finally, remember to keep in mind the long term effects of hazards, such as the affects of different dusts on the respiratory system or long term noise exposure.
Take account of the following hazard examples:
- Physical: e.g. lifting, awkward postures, slips and trips, noise, dust, machinery, computer equipment.
- Mental: e.g. excess workload, long hours, bullying.
- Chemical: e.g. asbestos, cleaning fluids and aerosols.
- Biological: e.g. hepatitis and other infectious diseases.
Step 2: Who might be harmed and how?
Now we know what the hazards are, we need to make the decision as to who may be harmed. This can include employees, contractors, customers, the general public or anyone who may be harmed by the activities of your organisation.
It's important to remember that not all workers have the same requirements, a few examples of this include pregnant women, people with disabilities, people who work from home and migrant workers.
We can't forget about those who might not be onsite all of the time such as maintenance staff, contractors, customers, or members of the general public.
With the rise of co-working space and shared offices, warehouses and shops you need to consider any other business which you may impact upon, by the same token they should be taking you into consideration when carrying out their own risk assessments. Speaking to each other is the best way to address any concerns you may have about the respective hazards created and the controls required.
Finally, and importantly hold talks with your workforce as, at the end of the day they're the experts. Review your risk assessment with them to see if you've missed any hazards or address any further concerns.
Step 3: Evaluate and action
We're over half way, we're doing well. Now we need to make the decision as to how likely harm is to occur, essentially the level of risk presented by the hazard. It's important to remember that you aren't expected to remove all risks entirely. However you are expected to know what the risks are and how you are going to manage them.
You have to do what is considered to be reasonably practicable. This is creating a balance between the level of risk, resources spent (including monetary, time and trouble). You don't need to take action if resources spend would be overly disproportionate to the end level of risk.
Your risk assessment will only ever include risks you can be reasonably expected to know, we may be good, but we're not psychic. The following bullet points are worth taking into account when carrying out your evaluation and action phase:
- Ask yourself - Can I remove the hazard entirely? If not, how can I reduce the potential harm to the minimum?
- Options include: Trialling different methods of working, blocking access to the hazard, issuing PPE, organising working patterns which reduce exposure to hazards for long periods of time,
- Provide 'welfare facilities', these can include first aid and eyewash stations, or hygiene stations.
When implementing health and safety practices and precautions, you needn't break the bank in doing so, nor do they need to be horrendously complicated. For example, placing a traffic mirror on a blind corner, the appropriate signage in hazardous areas or speed reduction ramps around car parks aren't expensive but can save you a lot in the long run.
Finally we strongly recommend you involve your workforce in this process. They are the experts doing the job and will quite often have some of the best ideas to implement in risk reduction. They also may have seen hazards that you haven't. Involving your workforce is also vital in creating a positive safety culture.
Step 4: Keeping a record
So, remember that if you have fewer than five employees, legally you don't have to write anything down, but it can be useful as a reference at a later date. What specifically do we need to write down?
- Specific hazards
- How these hazards can cause harm
- The controls currently in place
- New controls
If you have more than five employees you must keep a written record.
Keep your records simple, for example:
- Blind bend, traffic mirror fitted, cleaned regularly

- A thorough check was carried out
- You looked at who would be affected
- You took steps to eliminate or reduce risk as far as reasonably practicable
- You consulted your workforce or their representatives
- Risks ranked in order of importance
If your work changes fairly frequently, or the workplace changes or develops, (prime examples a construction sites or production factories) or if workers are moving from site to site (such as home care workers), your risk assessment must focus on a broader range of risks which could occur.
A couple of points to remember, when we're considering the actions for the bigger risks, we should be looking at long-term solutions. In the mean time, until these long-term solutions are in place, temporary measures will be required. The more harm a risk presents, the more we may need to invest in controls.
Step 5: Review and update
Every workplace, sooner or later, for better or worse, changes. These changes could include new equipment, a change of (or additional) locations, new products or services offered or countless other minor and major changes. But at what stage do we review our risk assessment?
- Period review - depending on the risk level of your organisation, this may vary but we would generally recommend an annual risk assessment. Even if there aren't any major changes, staying up to date is important.
- Material changes to your workplace which include any one or more of the following:
- Any significant changes?
- Have incidents not declined even though you have implemented controls?
- Has a member of your workforce or one of their representatives come to you with an issue?
The Necker Cube
A basic optical illusion, dating back to 1832, published by Swiss crystallographer Louis Albert Necker, a simple wire frame of a cube without any visual cues as to its orientation. This illusion can be interpreted in two ways, with either the lower-left or the upper-right square as its front side.
Originally the necker cube served as evidence of the human brain being a neural network with two distinct equally possible interchangeable stable states. In Robert J Sawyer's fiction book Factoring Humanity, 'Necker' became a verb. To force your brain to switch from one perspective to another.
At this stage you're probably wondering why I'm talking about it at all. The necker cube is a great tool when it comes to carrying out risk assessments. You need to make a conscious shift into another way of thinking. For example in our day to day lives most people wouldn't notice certain potential slips, trips or falls, but if you enact the Necker method you are shifting your pattern of thinking to 'could this corner create a hazard?'.
To sum up...
That thirty minutes I was allotted to carry out my first risk assessment, just wasn't going to happen. I muddled my way through it and when I finally completed it two and a half hours later, the school had decided not to go to a restaurant!
In the end though, the five step risk assessment isn't about creating paperwork, it is about keeping everyone safe:
- Hazard Identification
- Who might be harmed and how?
- Evaluate and action
- Keeping a record
- Review and update
Give the Necker method a try.
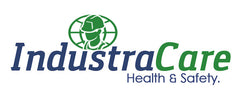